Mudar a posição de um equipamento dentro da fábrica para reduzir o tempo de deslocamento ou separar células de uma máquina para agilizar a manutenção. Às vezes são mudanças aparentemente simples e de baixo custo que transformam a história de uma empresa. A manufatura enxuta, também chamada de lean manufacturing, nasceu no Japão na década de 1950 e traz resultados para indústrias brasileiras até hoje.
A metodologia lean é um sistema de gestão que busca aumentar a eficiência e a produtividade da produção industrial evitando desperdícios. Ela é importante para melhorar a competitividade das empresas. Seus pilares são: eliminar desperdícios, melhoria contínua, compromisso com a qualidade da produção e a produção just in time, onde é produzido apenas o necessário e na quantidade necessária.
Reduzir custos, produzir mais com menos, incorporar as novas tecnologias nos processos e ter trabalhadores qualificados são preocupações comuns dos empresários no país. Lançado em novembro do ano passado, o novo Brasil Mais Produtivo tem a meta ambiciosa de apoiar 200 mil micros, pequenas e médias empresas do setor industrial na superação desses desafios – dessas, 93 mil terão atendimento presencial do Serviço Brasileiro de Apoio às Micro e Pequenas Empresas (Sebrae) e do Serviço Nacional de Aprendizagem Industrial (SENAI).
Além de diagnóstico gratuito, o programa federal oferece serviços de consultoria, educação profissional e apoio financeiro para melhorar a gestão, otimizar processos e promover o uso de tecnologias na empresa, pilares indispensáveis para a competitividade dos negócios.
Dentro do programa, a meta do SENAI e do Sebrae é atender 33 mil empresas nas consultorias manufatura enxuta e eficiência energética até 2027. Mais de 2,9 mil indústrias já se cadastraram nessa categoria.
Do tear aos carros: a origem do lean manufacturing
Talvez você conheça a Toyota pelos carros, mas a empresa japonesa começou sua produção em 1926 com teares automáticos. Na década de 1950, pós-segunda guerra mundial, o engenheiro Taiichi Ohno desenvolveu o “Sistema Toyota de Produção” para melhorar a produtividade e fazer frente à indústria automobilística dos Estados Unidos.
O termo enxuta (do original em inglês lean) foi incluído no final dos anos 1980 por pesquisadores do International Motor Vehicle Program (IMVP), ligado ao Massachusetts Institute of Technology (MIT), nos EUA.
Quando a manufatura enxuta está em cada detalhe: a jornada da Cedro
Em outra indústria têxtil, mas no Brasil, o lean também fez sua transformação. Em atividade desde 1872, a Cedro entrou nesse universo há 17 anos, quando começou a aprender o olhar crítico com cada etapa do processo produtivo para melhorar a performance.
Em 2016, a empresa tinha 16 milhões de metros de estoque e atendia 80% das entregas no prazo. Com as mudanças, o estoque caiu para entre 3 a 4 milhões de metros e o atendimento subiu para 94%.
“A Cedro antes da implementação do lean tinha uma produção empurrada, de produzir a sua capacidade total e procurar vender aquilo. Com o lean, fez essa inversão: primeiro vende e depois produz e produz com agilidade, qualidade, que a performance vai ser melhor”, conta Adriano Alves, coordenador de sistema de gestão integrado da empresa.
Para reduzir o estoque e mesmo assim aumentar a entrega foi feito todo um trabalho no processo produtivo. Um dos pontos de melhora foi a redução do tempo para transformar o algodão em tecido, de 100 para 40 dias, em média.
Outra alteração foi no uso da empilhadeira. Antes ela funcionava como um táxi: ia vazia até o operador e voltava cheia de material. Depois ela passou a funcionar como um ônibus, com rotas com pontos e horários determinados dentro da fábrica, em que no momento em que descia algum material também subia outro material em seguida.
Nas palavras do superintendente industrial da Cedro, Patrick Pinheiro, uma expressão chave do lean é “aprender a enxergar”, de modo que as pessoas percebam no dia a dia o que pode ser melhorado. “O processo não aconteceu de um estalo. Foram as próprias pessoas que já estavam aqui que foram treinadas, capacitadas para isso desde 2007 e fizeram toda essa transformação”, conta.
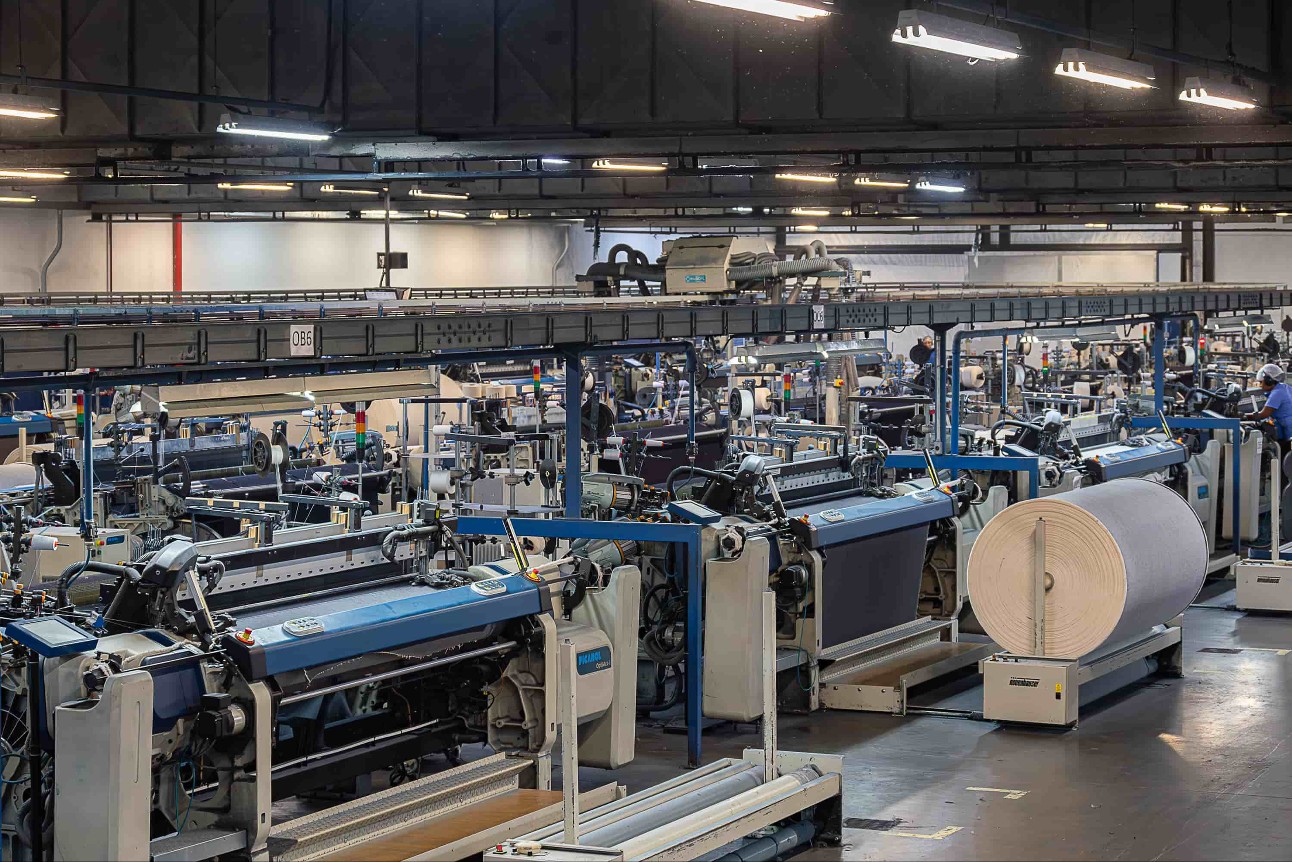
A partir de 2010, a empresa começou a incorporar o conceito de kaizen, que são melhorias sugeridas por quem está nas plantas produtivas, como aumentar a largura de um tecido que trouxe um diferencial competitivo ou flexibilizar o processo para que uma máquina possa ser usada em mais de uma etapa. As melhorias saltaram de 51 em 2010 para 18.848 em 2023.
Outro exemplo foi reaproveitar o vapor que era disperso na atmosfera como fonte de calor para água da caldeira. Isso gerou uma economia de R$ 15 mil por mês na geração de vapor e de R$ 1.600 em produtos químicos, além do reaproveitamento de 4,5 milhões de litros de água por ano.
Lembra dos números de redução de estoque? Para isso acontecer foi essencial reduzir o tempo de manutenção das máquinas. Antes elas ficavam paradas por 56 horas e precisavam de 45 funcionários. Depois que a empresa resolveu separar as células das máquinas para manutenção, são necessárias apenas 15 pessoas e 6 horas nesse processo.
Além dos resultados de produtividade, essa metodologia permite uma mais assertiva dos investimentos, focados no que é realmente necessário. “O dinheiro é a última etapa. Na hora que o operador não sai da máquina para buscar mais nada, que a máquina está na sua melhor performance, na maior velocidade, aí sim começa a se pensar em investimento financeiro. A grande maioria do processo de transformação das jornadas do lean não teve investimento alto. Foi realmente enxergar as coisas diferente”, completa Adriano Alves.
Manufatura enxuta nas pequenas: impulso de produtividade com apoio do SENAI
Hoje uma fábrica com 80 funcionários, a Biscoitos Itália começou com uma padaria no interior da Bahia, em São Miguel das Matas, na década de 1970. Foi o fato de ser um entroncamento rodoviário que levou o fundador da empresa a escolher Feira de Santana para ampliar os negócios. “Seu José Francisco gostou da cidade e viu que seria mais fácil se instalar, adquirir equipamentos e pessoas para trabalhar e resolveu fundar essa pequena empresa em 1978”, conta Geraldo Pires, diretor industrial e sócio da companhia.
O que começou com um turno de trabalho se transformou em dois e atualmente a fábrica funciona 24 horas por dia, em três turnos. E além do biscoito, passaram a fabricar também salgadinho de milho.
Em 2017, apareceram os ganhos de produtividade a partir de ajustes em processos produtivos e na promoção de capacitações com apoio do SENAI por meio do Brasil Mais Produtivo, programa do governo federal para impulsionar a competitividade.
Três anos depois, a Biscoitos Itália participou do programa de manufatura enxuta do SENAI Cimatec, em Salvador. A unidade conta com a primeira fábrica modelo de lean da América Latina.
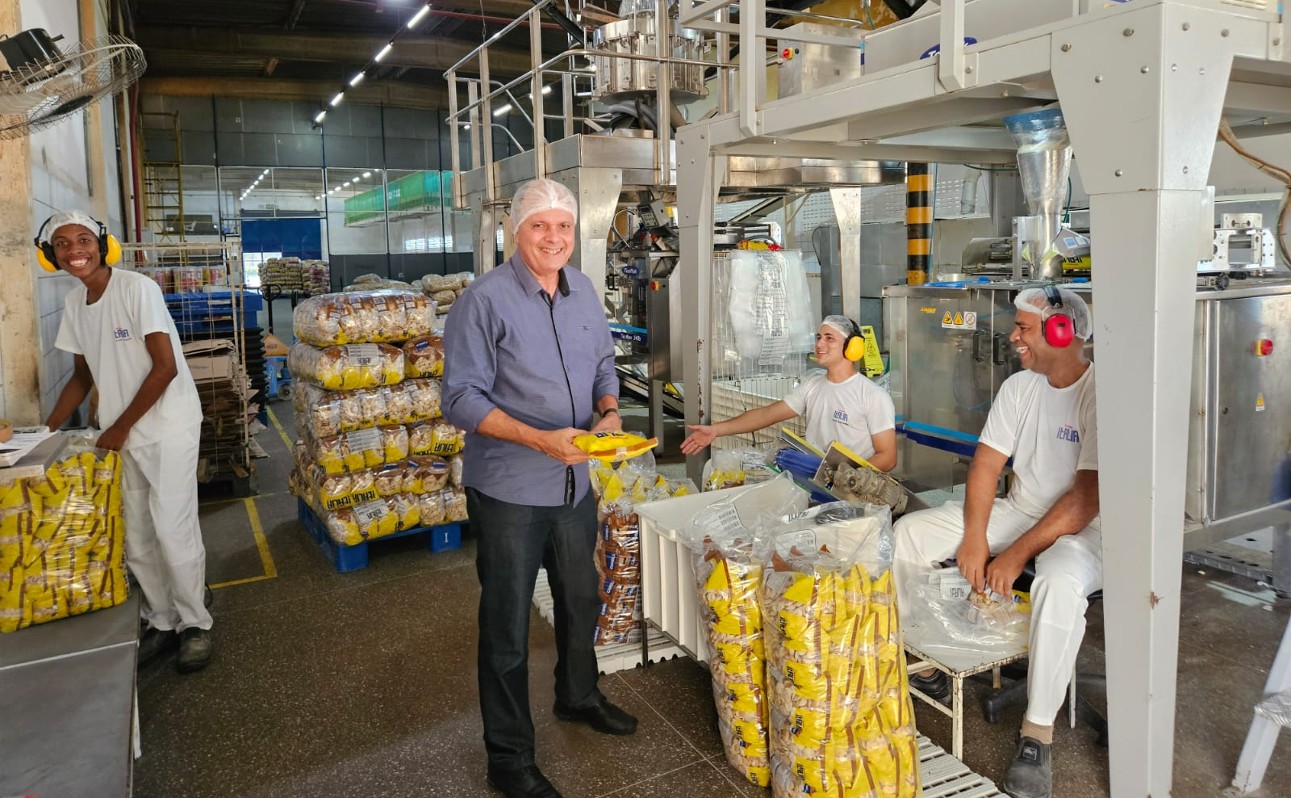
No programa, pequenas empresas são auxiliadas com conhecimentos da manufatura enxuta para resolver problemas do dia a dia. Uma dessas ferramentas é o diagrama de espaguete, que mapeia as movimentações feitas pelos funcionários na planta fabril para pegar ferramentas ou insumos, por exemplo.
“Tivemos uma boa melhora na produção do biscoito e no layout da fábrica, que inclui a posição de balanças, movimentação de pessoas e com a análise de espaguete a gente reduziu o tempo de deslocamento. Com pequenos investimentos mas com bom resultado”, afirma Geraldo Pires.
Em 2023, a empresa aderiu ao novo Brasil Mais Produtivo e conquistou um aumento de produtividade de 22% sem investimento financeiro. Foram feitas melhorias no empacotamento, posição de equipamentos, redução do tempo de deslocamento dos funcionários na planta e adaptação dos horários dos turnos.
“As máquinas de empacotar não davam conta do material produzido. A gente era obrigado a tirar a granel”, lembra o diretor da empresa. Por causa do ganho de produtividade, a estimativa é de uma economia de R$ 137 mil no ano. “Quem está de fora vê os gargalos da empresa e como as melhorias se adaptam a qualquer indústria. Isso é muito importante para gente que é pequeno e tem muitos gargalos”, completa Geraldo.
Fonte: CNI